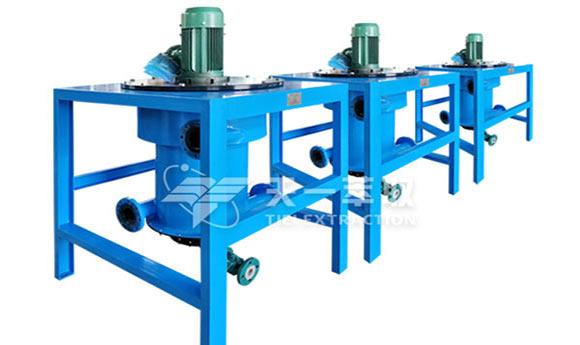
Solvent extraction of zinc is a hydrometallurgical technology for the efficient separation and purification of zinc, suitable for the treatment of zinc-containing leachate. The following is a detailed description of its process requirements and steps:
Solvent Extraction Zinc Process Requirements
Aqueous feed conditions:
pH value: usually adjusted to 1.5-2.5 (acidic conditions) to optimize the selectivity of the extractant (such as D2EHPA) for zinc.
Zinc concentration: The appropriate range is 5-30 g/L. Too low a concentration will reduce efficiency, and too high a concentration may require dilution.
Impurity control: Interfering ions such as Fe³⁺ (by oxidation/precipitation), Cu²⁺, and Cd²⁺ need to be removed in advance to avoid co-extraction.
Selection of extractants:
Common extractants: D2EHPA (high selectivity for zinc), Cyanex 272 (suitable for high pH), etc.
Organic phase composition: The extractant (5-20% vol) is dissolved in kerosene or sulfonated kerosene, and a phase regulator (such as isodecyl alcohol) is added to prevent emulsification.
Operating parameters:
O/A ratio: usually 1:1 to 3:1, adjusted according to zinc concentration.
Mixing time: 3-5 minutes to ensure adequate mass transfer.
Temperature: 25-40℃, high temperature may affect the stability of the extractant.
Stripping conditions:
Stripping agent: sulfuric acid (150-200 g/L) or hydrochloric acid.
Stripping pH: strong acidity (pH <1), which promotes the release of zinc from the organic phase.
Environmental protection and economy:
Organic phase recovery: recycle after regeneration to reduce loss.
Wastewater treatment: neutralize and precipitate heavy metals, and meet discharge standards.
Solvent Extraction Zinc Process
Pretreatment:
Filtration: Remove suspended matter from the leachate to avoid clogging of the equipment.
pH adjustment: Add acid (such as sulfuric acid) to adjust the pH to about 2.
Impurity removal: Oxidize Fe²⁺ to Fe³⁺ and hydrolyze and precipitate, or remove Cu and Cd by sulfide precipitation.
Extraction:
Mixing: The aqueous feed and the organic phase are contacted in the mixer settler, and the zinc is extracted into the organic phase.
Phase separation: The zinc-containing organic phase (loaded organic phase) is separated from the aqueous phase (raffinate) by standing.
Washing (optional):
Removal of entrained impurities: Wash the loaded organic phase with dilute acid or water to reduce co-extracted impurities.
Stripping:
Acid stripping: The loaded organic phase is mixed with concentrated sulfuric acid, and the zinc is transferred to the aqueous phase to form a zinc-rich solution (such as ZnSO₄ solution).
Phase separation: Separate the lean organic phase (circulated after regeneration) and the zinc-rich solution (sent to electrolysis or crystallization).
Organic phase regeneration:
Acid washing/alkali washing: Treat degradation products and restore extraction capacity.
Supplementary extractant: Add new extractant regularly to maintain concentration.
Subsequent treatment:
Electrolysis: electrolysis of zinc-rich solution to produce metallic zinc.
Crystallization: evaporation and concentration to obtain zinc sulfate crystals.
Solvent Extraction Zinc Extraction Equipment
Centrifugal Extractor is a fast and high-speed liquid-liquid extraction and separation equipment. It is essentially different from traditional extraction equipment such as mixer settler and extraction column in working principle. The centrifugal extractor uses a motor to drive the drum to rotate at high speed. Two liquids with different densities and immiscible with each other complete mixed mass transfer under the shear force generated by the rotation of the drum or blades, and are quickly separated under the centrifugal force generated by the high-speed rotation of the drum.
- Low power consumption: The motor power of the traditional 650 centrifugal extractor is 37.0KW. On the premise of ensuring the extraction rate and separation effect, the motor power of the new CWL650-M centrifugal extractor is 4KW, and the power consumption is about 1/10 of the traditional model.
- No vulnerable parts: The new centrifugal extractor adopts an upper suspension structure, which cancels the bottom machine seal of the traditional model, thereby completely solving the problem of bottom leakage and easy damage of the machine seal of the traditional model.
- Simple and stable structure: The design of the new centrifugal extractor simplifies the machine body, making it easier to operate and running more smoothly.
- Weir plate replacement: The new centrifugal extraction can realize the rapid replacement of the heavy phase weir plate.
Solvent extraction can achieve high efficient recovery of zinc (>95%) and produce high-purity products (electrolytic zinc up to 99.99%), and is one of the important technologies for green hydrometallurgy. Solvent extraction of zinc technology is a breakthrough solution in the field of hydrometallurgy, with high separation efficiency, low energy consumption, high recovery rate and environmental protection. Welcome contact us for more details.
Email: sales@tieiextraction.com
Whatsapp: +86 19069612820