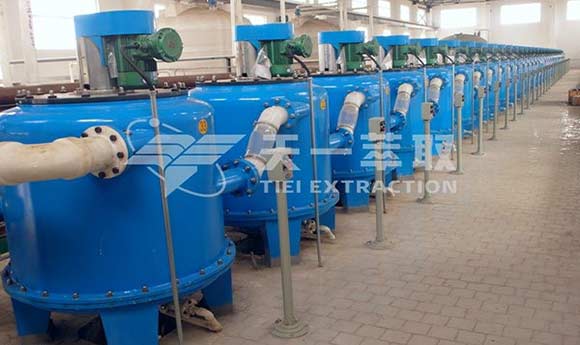
Vanadium is recovered from secondary resources such as vanadium-rich iron slag, waste vanadium catalyst, and stone coal ash. The process includes vanadium leaching, vanadium extraction, and vanadium precipitation. The commonly used methods for vanadium extraction are chemical precipitation, solvent extraction, and ion exchange.
Among them, the solvent extraction method has low production cost, fast equilibrium speed, renewable and recyclable organic phase, and easy to operate and realize automatic control, high vanadium recovery rate and purity, and large processing capacity. It can make up for the shortcomings of ion exchange and chemical precipitation in terms of environment, economy, and production capacity, and has received special attention.
The existing vanadium extraction technology is subject to certain restrictions in its application because of its improper treatment of industrial "three wastes", which can easily cause environmental pollution, and there are problems such as low single-stage extraction efficiency, cumbersome multi-stage extraction, and large loss of extractants.
The new vanadium extraction process launched by Zhengzhou Tiei Extraction can greatly avoid environmental pollution, improve the utilization rate and vanadium extraction rate, and simplify the process flow. Its production method is:
- Obtain the extract liquid. The vanadium-containing spent catalyst is ground, water-leached, and reduced acid-leached, and the water-leaching liquid and the reduced acid-leaching liquid are combined as the extraction stock liquid.
- Adjust the pH. Add potassium hydroxide liquid to the extract liquid to adjust its pH value.
- Saponification. The extractant is p204, the phase regulator is octanol, and the diluent is 260 solvent oil. The main extractant p204 is saponified with sodium hydroxide, and the saponification rate is 70% to 80%.
- Extraction. The liquid and the extractant are fed into the heavy phase feed port and the light phase feed port of the CWL-M centrifugal extractor respectively in a certain ratio, and a single-stage extraction is performed to obtain an extraction phase and a raffinate phase containing tetravalent vanadium.
- Stripping. Add sulfuric acid as a stripping agent to the extract phase, stripping is performed to obtain a stripping organic phase and a stripping aqueous phase.
- Precipitate vanadium. Add ammonia water to the stripping aqueous phase, adjust its pH value, stir at 70-90°C for 45-55 minutes to obtain hydrated vanadium dioxide precipitate, and wash the precipitate with clean water and calcine to obtain the product vanadium pentoxide.
- Calcination.
This process uses a single-stage extraction method to extract the raw liquid, concentrates the tail liquid, and extracts it separately. The single-stage extraction rate is as high as 96.4% or more. The extracted tetravalent vanadium can be precipitated without oxidation, avoiding the occurrence of atmospheric pollution caused by chlorine gas produced by vanadium oxidation by chlorate, improving the extraction capacity, utilization rate and vanadium extraction rate of the extractant, while also reducing the number of extraction stages and oxidation steps, simplifying the process, reducing production costs, and achieving significant economic benefits.
The use of saponified P204, which has low water solubility, high solubility in diluents, high stability, low price and easy availability of complexes with metals, together with 2-octanol and No. 260 solvent oil as extractants for single-stage extraction of the extract liquid not only improves the extraction rate and increases the vanadium-iron separation effect, but also effectively avoids the influence of iron, phosphorus and arsenic on the purity of the extracted vanadium. This not only reduces part of the impurity removal work, but also saves raw material consumption, and can directly prepare high-purity vanadium products.
Email: sales@tieiextraction.com
Whatsapp: +86 19069612820