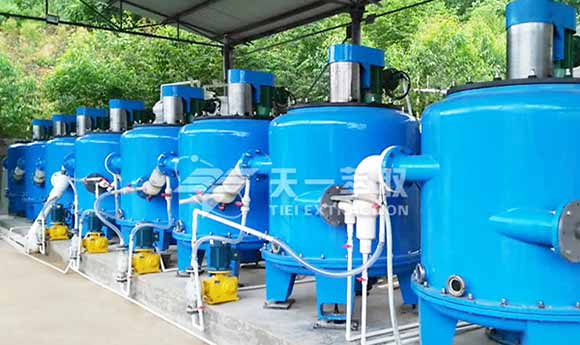
Overview of Ionic Rare Earth Ore Extraction
The grade of ion-adsorbed rare earth is very low, generally 0.03-0.1%, and it is impossible to enrich rare earth using conventional ore dressing methods. Currently, ammonium sulfate leaching is mainly used for recovery in industrial production. Ionic rare earth ore is leached with ammonium sulfate, and impurities such as aluminum and iron are removed with ammonium bicarbonate. After solid-liquid separation, the leaching liquid is further precipitated with ammonium bicarbonate or oxalic acid. The obtained rare earth carbonate or oxalate is then roasted to obtain a mixed rare earth oxide concentrate with a rare earth content of about 90%.
Due to the low rare earth concentration in the rare earth leaching liquid, the high consumption of ammonium bicarbonate and oxalic acid during the impurity removal and precipitation process, and the inevitable generation of a large amount of ammonia nitrogen wastewater, oxalic acid and high-salinity wastewater discharge, which seriously pollutes the environment. Moreover, due to the relatively complex process of rare earth recovery by precipitation, the intermittent manual operation leads to a high rare earth loss rate, and the high consumption of chemical materials, resulting in high production costs. In addition, the rare earth oxide concentrate obtained by precipitation recovery of rare earths contains 10% impurities such as iron, aluminum, calcium, silicon and trace radioactive nuclides. After dissolution with hydrochloric acid, the above impurities are enriched in the slag, resulting in the acid-soluble slag radioactivity exceeding the standard. It is necessary to build a warehouse for storage in accordance with the regulations for the disposal of radioactive waste residues, which poses a safety hazard.
Therefore, low-concentration rare earth leaching liquid in ionic rare earth ores, as well as low-concentration rare earth liquid in mine leaching tailings and tailings leachate, all have the problems of complex enrichment processes, low rare earth recovery rates, and high recovery costs. Therefore, it is urgent to develop green, efficient, and low-cost enrichment and recovery technologies for low-concentration rare earth liquid, improve the utilization rate of rare earth resources, and solve the problems of environmental pollution in the process of rare earth resource recovery.
Rare earth green extraction and separation technology
In response to the resource and environmental problems faced by the rare earth industry, Professor Huang Xiaowei of Beijing Research Institute of Nonferrous Metals and YUYAN Rare Earth New Materials Co., Ltd. led a team to invent a new technology for efficient and green extraction and separation of ionic rare earth ores. The low-concentration rare earth liquid was subjected to the first centrifugal extraction using a non-saponifiable organic extractant to obtain the first rare earth-loaded organic phase and the first raffinate. The first loaded organic phase was subjected to the first centrifugal stripping using an inorganic acid to obtain the first rare earth-enriched liquid. The rare earth liquid extraction and enrichment method is simple to operate, has a high rare earth recovery rate and low recovery cost, and the rare earth recovery rate is 98.8%. The centrifugal extraction host equipment uses Zhengzhou Tiei Extraction CWL-M series centrifugal extractors, with extraction and stripping stages of 2 to 8, respectively. As the number of stages increases, the rare earth extraction rate and stripping rate will increase, preferably 3 to 5.
Advantages of rare earth green extraction and separation technology
1.Simplify the process flow, improve the rare earth recovery rate, reduce pollutant emissions and reduce costs.
By directly performing non-saponification centrifugal extraction and centrifugal stripping on low-concentration rare earth liquid under high flow ratio conditions, efficient rare earth enrichment can be achieved (a mixed rare earth liquid with a ReO content of more than 200g/L can be obtained), and the enrichment ratio is as high as 200 or more. Compared with ammonium bicarbonate precipitation enrichment technology, the process of rare earth green extraction and separation technology is greatly simplified, rare earth loss can be reduced by about 10%, no ammonium bicarbonate and oxalic acid are consumed, environmental pollution is avoided, and production costs are greatly reduced. In addition, the initial separation of medium and heavy rare earths and light rare earths can be achieved, providing more convenient conditions for subsequent rare earth extraction and separation.
2.Good impurity removal effect
In the existing technology, before rare earths are enriched and recovered, ammonium bicarbonate is used to neutralize and remove impurities from low-concentration rare earth liquid to remove impurities such as iron or aluminum. However, this technology effectively controls the contact time of the two-phase mixture, that is, the rare earths with fast mass transfer rates basically reach the kinetic and thermodynamic equilibrium state of the mass transfer process, and are thus efficiently extracted into the organic phase, while the impurity ions such as iron and aluminum with slow mass transfer rates are far away from the kinetic and thermodynamic equilibrium state of the mass transfer process, and are basically not extracted (the extraction rate of iron and aluminum is less than 5%), and remain in the aqueous phase, thereby achieving effective separation of rare earths and impurities such as iron or aluminum, which not only saves the steps of neutralization and impurity removal, but also does not consume ammonium bicarbonate, thereby reducing production costs and environmental pollution.
3.Less loss of organic phase
By rationally optimizing the two-phase mixing and centrifugal phase separation time and mixing intensity during the centrifugal extraction and stripping process, the two-phase separation effect is improved while ensuring the rare earth extraction rate, reducing the loss of the organic phase. In addition, the raffinate is deoiled by using alkali metal, alkaline earth metal carbonate or basic carbonate, so that the organic extractant entrained or dissolved in the raffinate can be effectively recycled, and the organic phase recycling rate reaches more than 98%. The organic phosphorus content in the raffinate after deoiling is less than 1mg/l, meeting the national environmental protection standards.
4.High extraction and enrichment efficiency
P507 and P227 are both acidic phosphorus extractants. To extract one rare earth ion, three hydrogen ions must be replaced. As the acidity of the aqueous phase increases, the rare earth extraction rate decreases, that is, the rare earth extraction rate is inversely proportional to the acidity of the aqueous phase. For rare earth liquid with a rare earth concentration higher than 1g/l, first use P507 to extract medium and heavy rare earths, and then adjust the acidity of the aqueous phase of the raffinate, and further use P507 to extract light rare earths, thereby achieving the effect of improving the rare earth extraction rate (>99), and the rare earth concentration is enriched by about 500 times.
5.Compared with traditional extraction methods, it reduces the investment in equipment and raw materials.
In the process of extracting trace rare earths from low-concentration rare earth liquid, the volume of the aqueous phase is large, and extraction equipment with a large flow ratio and high processing volume is required. When using a mixer settler or extraction column, the equipment is large in size and occupies a large area, and the required organic input is large. However, the centrifugal extraction equipment is small in size and small in organic input, which is only 1/30 to 1/10 of that of the traditional extraction equipment.
Email: sales@tieiextraction.com
Whatsapp: +86 19069612820