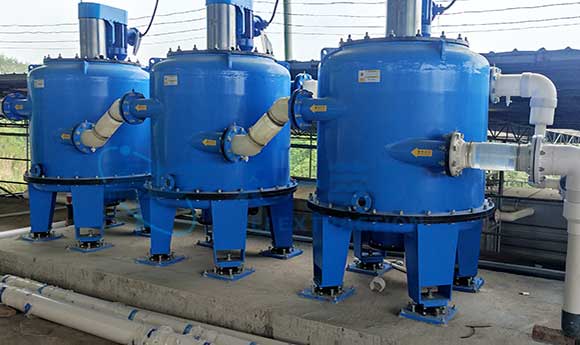
A series of original rare earth smelting and separation technologies have been developed for different rare earth resources, which are widely used in industrial production and have made China a major rare earth producer in the world.
At present, the mainstream processes for rare earth smelting and separation include:
- Concentrated sulfuric acid decomposition--water leaching--P204 or carbon-ammonia transformation--saponification P507--HCL system extraction and separation
- Oxidative roasting--hydrochloric acid leaching--alkali conversion to optimal solution--saponification P507--HCL system extraction and separation
- Ammonium sulfate leaching--carbon-ammonia precipitation--hydrochloric acid leaching--saponification P507, cyclohexane acid system extraction and separation
The annual production capacity of the three processes exceeds 300,000 tons, accounting for about 85% of the world's total, of which more than 90% uses solvent extraction and separation, and the product purity is 2N-5N.
In response to the resource and environmental problems faced by the rare earth industry, Professor Huang Xiaowei of Beijing Research Institute of Nonferrous Metals and Yunnan Rare Earth New Materials Co., Ltd. led a team to systematically carry out basic theoretical research on rare earth green separation chemistry. They proposed a number of new ideas, such as using calcium magnesium alkaline earth metals instead of alkali metals or ammonium, and non-equilibrium centrifugal extraction instead of precipitation to enrich, recover and separate and purify rare earths. They invented a new technology for efficient and green extraction and separation of ionic rare earth ores, which reduces ammonia nitrogen and radioactive nuclide pollution at the source and efficiently recycles water and materials. It is a new clean production process technology.
There is a problem in the industrial application of the above rare earth extraction new process, that is, the extraction flow ratio is 20-50, and the conventional extraction equipment is bulky and has low production efficiency, and it is impossible to achieve high flow ratio and high throughput operation. Zhengzhou Tiei Extraction has launched a patented product with independent intellectual property rights for rare earth metal extraction technology -- centrifugal extractor, which perfectly realizes the high flow ratio industrial rare earth ore extraction, with an extraction rate of >98.5%.
Zhengzhou Tiei Extraction Centrifugal Extractor has been successfully applied in rare earth concentration production lines. It not only solves the technical problems of low resource recovery rate and serious pollution of three wastes in the process of leaching, enrichment, separation and purification of ionic rare earth ores, but also greatly reduces the operating cost of equipment and manpower output cost, and effectively promotes the further development of rare earth green development technology.
Email: sales@tieiextraction.com
Whatsapp: +86 19069612820