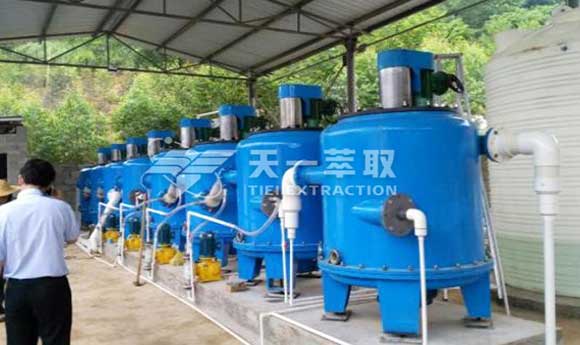
With the continuous advancement of industrial technology, the effective recycling of resources has become increasingly important. As a key strategic metal, vanadium is widely used in many fields such as machinery, shipbuilding, railways, aviation and batteries. Especially in steel production, more than 90% of vanadium is added to steel in the form of alloys to improve its performance. However, traditional vanadium extraction methods such as sodium roasting and calcium roasting have problems such as high cost and low efficiency, and more environmentally friendly and efficient alternatives are urgently needed.
In recent years, the development of hydrometallurgical technology has brought new opportunities for vanadium extraction from vanadium slag. Among them, the direct leaching vanadium extraction process combined with solvent extraction has become an effective way to improve the vanadium recovery rate. In particular, the extractant P507 has shown great potential in the field of vanadium extraction with its excellent selectivity and low cost. However, traditional reactors and box-type extraction equipment have the disadvantages of large footprint, intermittent operation, and long residence time, which limits the improvement of production capacity. To solve these problems, the CWL-M centrifugal extractor came into being and gradually became a star equipment in the vanadium extraction process.
Advantages of CWL-M centrifugal extractor
- Efficient processing capacity. CWL-M centrifugal extractor adopts advanced centrifugal technology, and fully mixes the two-phase liquid through the strong shear force generated by high-speed rotation, thereby realizing a fast and efficient mass transfer process. Compared with traditional equipment, it not only greatly shortens the processing time, but also improves the extraction efficiency.
- Easy to operate continuously: The equipment is compactly designed, easy to install and maintain, and is particularly suitable for large-scale continuous production. In addition, due to its unique structural characteristics, it can effectively avoid the common phase separation difficulties of traditional equipment, ensuring the stability and reliability of the entire extraction process.
- Reduce material loss: CWL-M centrifugal extractor has a small liquid storage volume, which means that the amount of organic solvent required during operation is relatively small, which helps to reduce operating costs. At the same time, the good separation effect also reduces the mutual entrainment phenomenon between materials, further reducing losses.
- Strong flexibility: In addition to being able to be used alone, CWL-M centrifugal extractor can also be configured in series or parallel according to actual needs to form a multi-stage countercurrent extraction system, thereby meeting vanadium extraction tasks under different scales and requirements.
Application Case Analysis of CWL-M Centrifugal Extractor
Tiei Extraction conducted an experimental study on the vanadium-containing liquid obtained by leaching vanadium-containing steel slag from a steel plant using titanium dioxide waste acid. It was found that under certain conditions (such as a controlled speed of 2800r/min and a two-phase flow ratio of O/A=2/1), the use of a CWL-M centrifugal extractor can achieve a vanadium extraction rate of more than 99.5%. This result far exceeds the effect that can be achieved by conventional methods, fully demonstrating the powerful advantages of the new centrifugal extraction technology.
With its excellent performance, the CWL-M centrifugal extractor has shown broad application prospects in the field of vanadium extraction. It not only solves many shortcomings of traditional equipment, but also provides enterprises with a more economical and efficient solution. If you have any needs, welcome consult us.
Email: sales@tieiextraction.com
Whatsapp: +86 19069612820