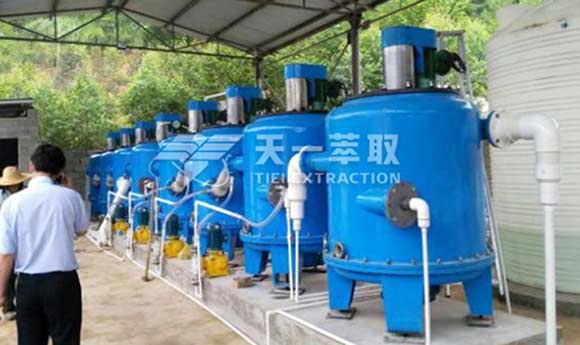
As the third metal under electrification, nickel for power batteries will usher in explosive growth with the explosion of terminal demand for new energy vehicles and the gradual advancement of high nickelization. Among the global onshore nickel resources, about 60% exist in the form of laterite nickel ore. With the development of more and more laterite nickel ore projects, the properties of laterite nickel ore resources are becoming more and more understood. At present, the smelting process of laterite nickel ore includes two major directions: pyrometallurgy and hydrometallurgy. Generally, pyrometallurgy is suitable for siliceous-magnesia nickel ore with relatively high nickel content, and hydrometallurgy is suitable for limonite-type nickel ore with relatively low nickel content.
Hydrometallurgy of laterite nickel ore adopts HPAL high pressure acid leaching
The hydrometallurgical processes of laterite nickel ore mainly include reduction roasting-ammonia leaching (Caron process), high pressure acid leaching (HPAL), and atmospheric pressure acid leaching (AL). The three hydrometallurgical processes are respectively suitable for laterite nickel ores with different MgO contents. Since MgO will cause unnecessary consumption of acid in the reaction, thereby increasing costs, HPAL is generally suitable for processing limonite ores with a Mg content of less than 5%.
Although HPAL has relatively harsh reaction conditions, strict equipment requirements, and a relatively high capital expenditure level, it is the current and future mainstream route and development direction of the hydrometallurgical process because of its obvious advantages in nickel and cobalt recovery rate and relatively low energy consumption and emissions.
High Pressure Acid Leaching Process
High pressure acid leaching process generally uses dilute sulfuric acid as the leaching liquid. Under high temperature and high pressure environment, nickel and cobalt enter the leaching liquid, most of the iron and silicon enter the slag, and are subsequently neutralized and impurity-removed and precipitated to obtain MHP (nickel cobalt hydroxide) or MSP (nickel cobalt sulfide).
The core of the HPAL process is to ensure that nickel and cobalt are fully leached under high temperature and high pressure reaction environment. The whole process is divided into four parts: feed preparation, high-pressure acid leaching, neutralizer CCD countercurrent washing, and precipitation.
After years of development, the HPAL process has made great improvements in process design. At present, the recovery rates of nickel and cobalt in the whole process can reach nearly 96% and 94%. HPAL process is the main direction of the future development of laterite nickel ore hydrometallurgical process.
High Pressure Acid Leaching Process Products
There are two main direct products of hydrometallurgy: nickel cobalt sulfide (MSP) and nickel cobalt hydroxide (MHP), which differ only in the final precipitation stage. MSP has a higher nickel-cobalt content, low water content and high purity, while MHP has lower cost, better preparation process safety, and is easy to produce nickel sulfate.
Nickel cobalt hydroxide (MHP) - acid dissolution - impurity removal - extraction → nickel sulfate product
Nickel cobalt hydroxide is subjected to reduction acid dissolution leaching under the action of sulfuric acid and a reducing agent to obtain a leachate; catalyst, oxidant and neutralizer are added to the leachate to simultaneously perform catalytic oxidation reaction and neutralization reaction to obtain a first impurity removal solution; the first impurity removal solution is subjected to extraction and impurity removal, evaporation and crystallization to obtain nickel sulfate.
Core Technology of Extraction and Impurity Removal - CWL-M Green Centrifugal Extraction Process
The extraction of nickel-cobalt leaching solution from laterite ore has high requirements for equipment. It is necessary to select extraction equipment with stable performance, corrosion resistance, high extraction efficiency and good extraction effect. Zhengzhou Tiei Extraction has the CWL-M series centrifugal extractor, which is a green extraction process developed based on the cation exchange and complex extraction principles in metal extraction and the CWL-M new extraction equipment. It has the following characteristics:
1.High metal extraction rate, up to 99.9%.
2.Simple process flow and easy operation.
3.The quality of the stripping solution is stable and can meet different production requirements.
4.The residual amount of aqueous phase solvent after treatment is small, which can reduce the processing pressure of subsequent sections.
5.The extraction equipment occupies a small area and has great processing flexibility.
CWL-M centrifugal extraction equipment is a powerful tool for extracting nickel-cobalt leaching solution from laterite ore and has been successfully applied in industrial production. Welcome contact us for more details.
Email: sales@tieiextraction.com
Whatsapp: +86 19069612820