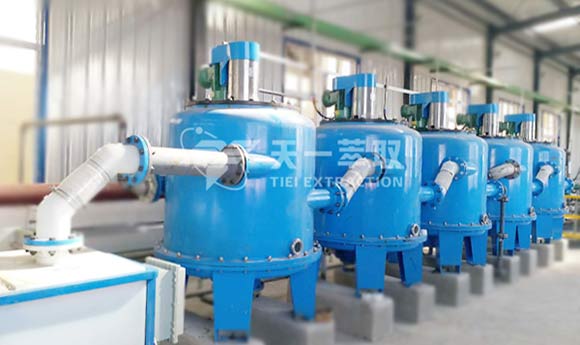
Extracting nickel and cobalt from laterite nickel ore is a hot topic recently, because with the explosion of terminal demand for nickel for power batteries and the gradual advancement of high nickelization, the market demand for nickel and cobalt will usher in explosive growth. Currently, about 60% of the world's nickel resources exist in the form of laterite nickel ore.
Process of extracting nickel and cobalt from laterite nickel ore
The smelting process of laterite nickel ore includes two methods: pyrometallurgy and hydrometallurgy. The pyrometallurgy is suitable for silicon-magnesium nickel ore with relatively high nickel content; the hydrometallurgy is suitable for limonite-type nickel ore with relatively low nickel content. Today, we will focus on introducing the hydrometallurgy extraction process of laterite nickel ore.
The hydrometallurgy extraction process of laterite nickel ore includes three types: reduction roasting-ammonia leaching, high-pressure acid leaching (HPAL), and atmospheric pressure acid leaching (AL). Among them, although the high-pressure acid leaching process has relatively harsh reaction conditions, strict requirements on equipment, and a relatively high capital expenditure level, it has obvious advantages in nickel and cobalt recovery rate and relatively low energy consumption and emissions. It is the current and future mainstream route and development direction of the hydrometallurgy method. The core of the high-pressure acid leaching process is to ensure that nickel and cobalt are fully leached under high temperature and high pressure reaction environment under the control of fine parameters. The entire process is divided into four parts: feed preparation, high-pressure acid leaching, neutralizer CCD countercurrent washing, and precipitation.
Equipment for extracting nickel and cobalt from laterite nickel ore
The equipment for extracting nickel and cobalt from laterite nickel ore recommends the use of CWL-M centrifugal extractor, which is a new, efficient and energy-saving liquid-liquid extraction and separation equipment independently developed and produced by Zhengzhou Tiei Extraction. Centrifugal extractors have been widely used in metal extraction and separation operations in the field of hydrometallurgy.
The working principle of CWL-M centrifugal extractor is essentially different from other traditional extraction equipment. The principle of the centrifugal extractor is to inject the light and heavy phase solutions into the centrifugal extractor in a certain proportion, and the two-phase liquids are quickly mixed and transferred in the equipment. Then, relying on the action of centrifugal force, the mixed liquid is separated according to the light and heavy phases and discharged from the body through different outlets to complete the two-phase separation process.
Process flow of centrifugal extractor for extracting nickel and cobalt from laterite nickel ore
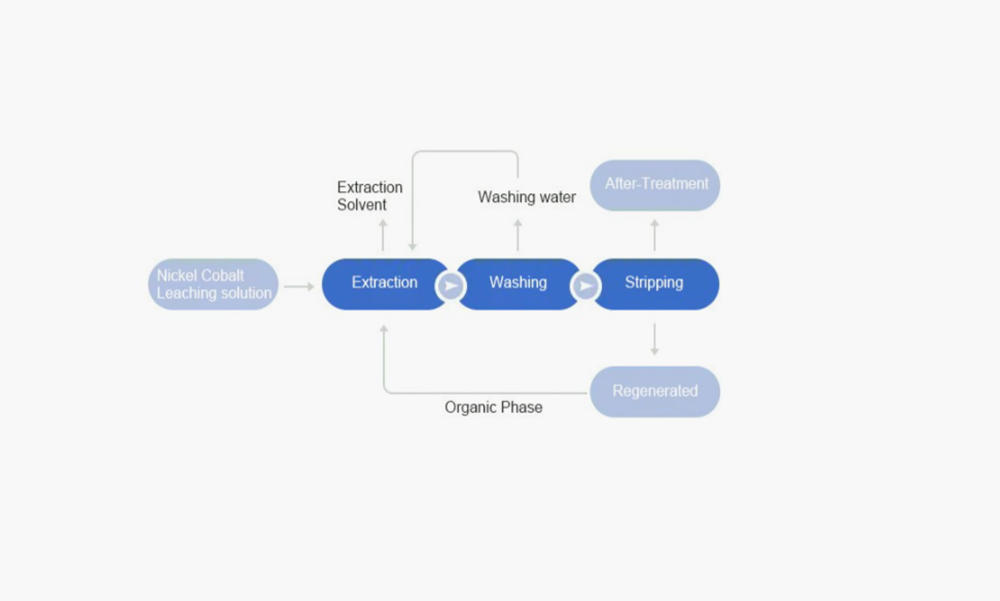
The above is a brief introduction to the process and equipment for high-pressure acid leaching of nickel and cobalt from laterite nickel ore. There are many models of CWL-M series centrifugal extractors, including small-scale laboratory extraction equipment and industrial extraction equipment. Customers can select equipment according to the processing volume. For more information and prices of centrifugal extractors, welcome contact us.
Email: sales@tieiextraction.com
Whatspp: +86 19069612820