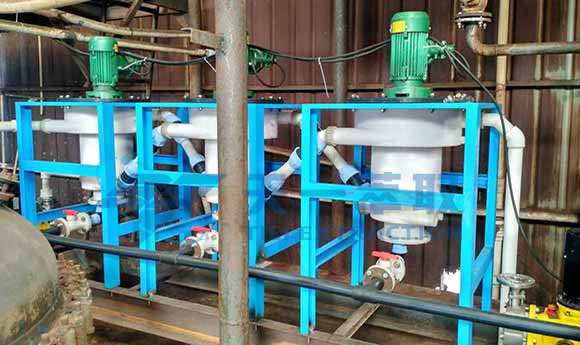
Indium is a rare metal, it is mainly used in the production of liquid crystal displays and flat screens because of its strong light permeability and electrical conductivity. 90% of the world's indium production comes from the by-products of lead and zinc smelters. The smelting recovery method of indium is mainly to recover it by enriching it from the smelting slag, slag and anode mud of copper, lead and zinc.
The extraction process of indium is mainly based on extraction-electrolysis, which is also the mainstream process technology for indium production in the world today. Its principle process flow is: indium-containing raw materials -- enrichment -- chemical dissolution -- purification -- extraction -- stripping -- zinc (aluminum) replacement -- sponge indium -- electrolytic refining -- refined indium.
In the process of indium extraction, the traditional extraction equipment used includes mixer settler, spray extraction towers and impinging stream-rotating packed bed extractors. For example, when the mixer settler is used as an extractor, the contact surface between the oil and water phases is small, the mass transfer coefficient is low, and the processing capacity is small. At the same time, due to the low separation strength, there are problems such as poor separation effect between the oil and water phases and large amount of solvent entrainment.
In view of the shortcomings of the above problems, Zhengzhou Tiei Extraction launched the CWL-M new centrifugal extraction process to extract indium from indium-containing leaching solution. In the process of extracting indium, the liquid inventory in the equipment is reduced and the separation efficiency is improved to solve the problems of large liquid inventory in the mixer settler, large floor space and low separation efficiency in the existing technology.
The CWL-M new centrifugal extraction process is mainly:
- Leaching: Mix the indium-containing material with sulfuric acid for leaching. After the leaching is completed, the liquid and solid are separated to obtain an indium-containing leachate.
- Reduction: Add reduced iron powder to the indium-containing leachate for reaction to obtain a reduced solution.
- Extraction: Add the extractant and the reducing solution to the CWL-M centrifugal extractor for extraction to obtain an extract. Among them, the extractant is a mixture of p204 (diisooctyl phosphate) and kerosene, and the volume ratio of p204 to kerosene is (2-3): (7-8); the volume ratio of the extractant to the reducing solution is (3-5): 1, that is, the volume ratio of the organic phase to the aqueous phase is (3-5): 1; the extraction process is carried out in the centrifugal extractor, using 3-5 level countercurrent extraction.
- Stripping: Add hydrochloric acid to the extract in the CWL-M centrifugal extractor for stripping to obtain a stripping solution containing an indium-rich organic phase; wherein the stripping process is carried out in the CWL-M centrifugal extractor, using 4-6 levels of countercurrent extraction; the hydrochloric acid concentration is 6-7 mol/l.
- Indium production: Add a reducing agent to the stripping solution for reaction, and replace to obtain sponge indium; alkali melt and ingot casting of the sponge indium to obtain an indium ingot containing 99.72% indium.
Advantages of CWL-M centrifugal extraction process
- The CWL-M centrifugal extraction equipment is used for indium extraction, with short mixing time and rapid contact between the two phases, which avoids solid precipitation and the third phase caused by long mixing time when the traditional mixer settler is used for indium extraction.
- The separation strength of the CWL-M centrifugal extractor is high, and the density difference between the oil and water phases is utilized. Under the action of high-speed rotating centrifugal force, the two phases can be separated quickly and effectively, with good phase separation effect and the use of organic phase regeneration.
- The CWL-M centrifugal extractor occupies a small area, which is only 1/5 of the traditional mixer settler, and the solution retention in the equipment is very small, reducing the investment cost of the organic phase.
- The CWL-M centrifugal extractor used is a fully sealed structure, with less organic phase volatilization and a good operating environment. It is simple to operate, has a high degree of automation, low energy consumption and large processing capacity. The equipment adopts an upper suspension structure, no bottom bearing and mechanical seal, no leakage risk, and simple and convenient maintenance.
CWL-M centrifugal extractor can reduce the amount of liquid in the equipment and improve the separation efficiency. If you also have a project in Hydrometallurgy area, welcome contact us adn we can provide professional technology and services.
Email: sales@tieiextraction.com
Whatspp: +86 19069612820