Oxalic acid is toxic, and the production wastewater seriously pollutes the water body and affects the environment. The rare earth ore oxalic acid containing wastewater was discharged into reservoirs and rivers, poisoning the fish in reservoirs and rivers.Oxalic acid is expensive. Oxalic acid required for the production of each ton of rare earth oxide is 1.6-2.2 tons, accounting for more than 45% of the production cost, which seriously affects the economic benefits of production.
In this regard, a process for directly producing rare earth chloride from the leaching solution of low concentration rare earth ores, especially the leaching solution of weathered crust leaching rare earth ores, is introduced by using 2-ethylhexyl phosphonic acid mono (2-ethylhexyl) ester (P507) as the extractant to extract rare earth elements, and then by using hydrochloric acid for back extraction. The process flow is as follows:
- Adjust PH. Remove iron, aluminum, lead, copper and other metal impurities from the leaching solution of rare earth ore containing low concentration rare earth elements, such as the leaching solution of weathered shell leaching type rare earth ore, by controlling the PH value
- Extraction. A multi-stage countercurrent extraction system consisting of mono (2-ethylhexyl) 2-ethylhexylphosphonate (P507) and sulfonated kerosene was used. The extraction process is 2 stages.
- Stripping. The loaded organic phase after extraction is subject to multi-stage countercurrent stripping with hydrochloric acid, and the stripping solution is concentrated to obtain the product of rare earth chloride. The organic phase after stripping is recycled after regeneration, and the process of stripping is 3 stages.
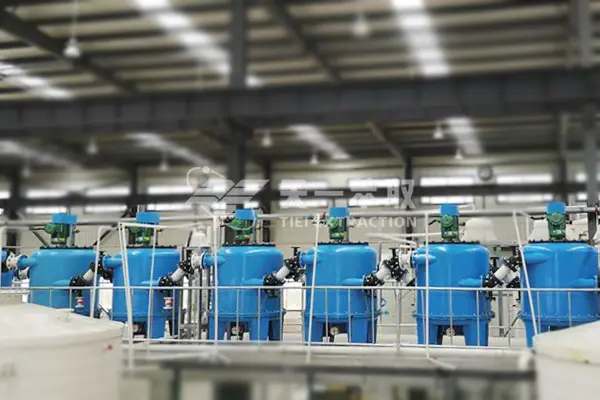
The whole extraction and stripping process is used by CWL-M series centrifugal extractor. The centrifugal extractor is selected as the equipment for extraction and stripping. Its mass transfer process is fast, and it is easy to achieve a high ratio during extraction and stripping, which can improve the concentration of rare earth elements in the stripping solution and reduce the concentration of rare earth elements in the subsequent sections.
The rare earth recovery rate of this process is more than 90%, and the process belongs to a closed system, without waste water pollution, with significant environmental benefits, stable process operation, easy control and continuous production, convenient adjustment of relevant parameters, and easy realization of automatic and continuous production