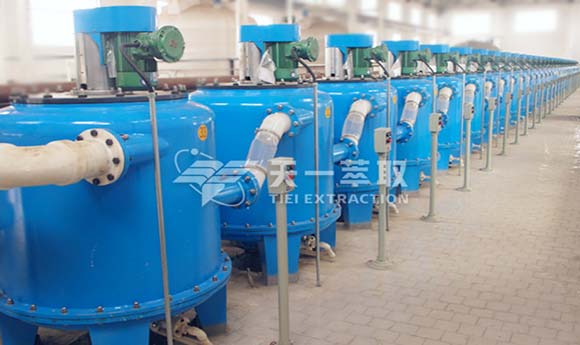
Ethyl acetate has low toxicity, volatile, and has a pungent odor at high concentrations. It is a widely used fine chemical product with excellent solubility and quick drying properties. At the same time, ethyl acetate is sensitive to air and absorbs water and slowly hydrolyzes to become acidic.
Ethyl acetate will not mix with water in any ratio (ethyl acetate and water are slightly soluble), but in the organic chemical, flavor and fragrance, paint, pharmaceutical and other industries, there will inevitably be waste liquid. Regardless of the direction of resource recycling and environmental integration treatment, the waste liquid needs to be treated, and the purpose of extraction and separation of the mixture of ethyl acetate and water will be used.
In order to recover acetonitrile and ethyl acetate from pharmaceutical waste, we generally adopt the process of pretreatment first and then extraction distillation. In this way, we can recover ethyl acetate from the waste liquid, and the ethyl acetate content reaches more than 98.5%.
In addition, we also have a relatively good separation effect for the extraction separation of ethyl acetate-ethanol-water system. After experimental analysis of the effects of factors such as suitable extractants, different solvent ratios and reflux ratios on product purity, the results show that the extraction separation method can be used to separate ethyl acetate-ethanol-water. When the solvent ratio is 1:1:1, high-concentration (99%) ethyl acetate can be obtained at one time, and 95% ethanol solution can be obtained at the same time. The yield of ethyl acetate reaches 97%, and the amount of water used in the separation process is only twice that of the raw material, with low energy consumption.
The extraction and separation device is indispensable in the implementation of the ethyl acetate extraction and separation process. Zhengzhou Tiei Extraction is a domestic service provider of liquid-liquid extraction and separation technology and equipment. It has been more than 10 years since the independent innovation, research and development and production of the first generation centrifugal extractors in 2009. The centrifugal extractors have also undergone many upgrades. The latest generation of CWL-M high-efficiency new centrifugal extractors currently launched have mature technology, not only with high extraction and separation efficiency, good separation effect, less entrainment, but also low power, only one-third of the power of traditional centrifugal extractors; the equipment adopts a fully enclosed design and continuous operation, and is currently the most ideal extraction and separation device for domestic and foreign applications.