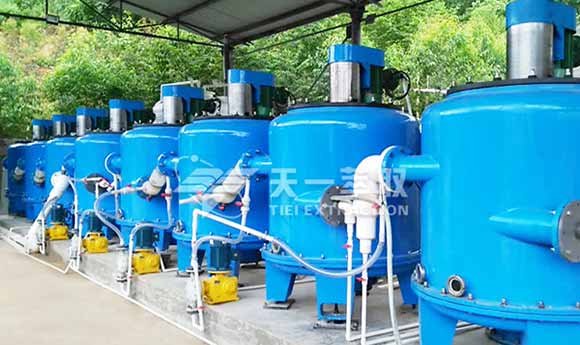
In ionic rare earth ores, rare earths exist in the weathering crust of granite in the form of ions. Rare earth leaching solution is obtained through in-situ leaching technology using ammonium sulfate or magnesium sulfate. However, the rare earth concentration in the obtained leaching solution is low, the chemical composition is complex, and the content of impurity ions is high.
At present, the main processes for enriching rare earths in leaching mother liquor include ammonium carbonate precipitation, oxalic acid precipitation, magnesium bicarbonate precipitation and solvent extraction.
The ammonium carbonate precipitation method has poor selectivity and is easy to form co-precipitation with other impurity ions, which makes the subsequent rare earth liquid purification and extraction separation process more difficult. At the same time, the precipitation mother liquor produced by the ammonium carbonate precipitation method contains a large amount of ammonia nitrogen wastewater, which pollutes the environment.
The rare earth recovery rate of the oxalic acid precipitation method is low and the conditions are harsh. At the same time, the oxalic acid consumption is large, the price is expensive, and it is a toxic substance.
When using solvent extraction to enrich rare earth leaching mother liquor, due to the dispersion, low grade and difficulty of extraction and separation of ionic rare earth resources, the traditional ionic rare earth ore leaching enrichment, separation and purification processes have problems such as low recovery rate, high consumption, and the generation of large amounts of ammonia nitrogen or high-salt wastewater and waste residue containing radioactive substances that seriously pollute the environment, which restricts the healthy and circular development of the rare earth industry.
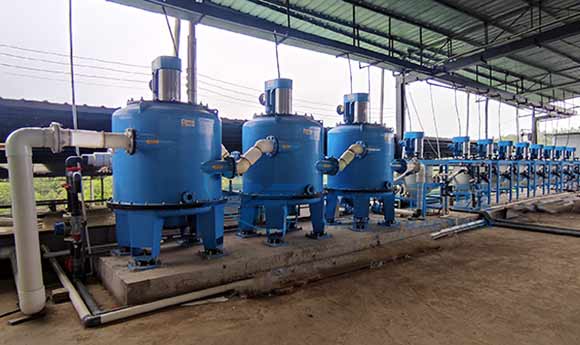
In order to solve the problem of enriching rare earth leaching mother liquor by solvent extraction, Academician Huang Xiaowei from Beijing Research Institute of Nonferrous Metals and YOUYAN Rare Earth New Materials Co., Ltd. led a team to systematically carry out basic theoretical research on rare earth green separation chemistry. They proposed a number of new ideas, such as using calcium magnesium alkaline earth metals instead of alkali metals or ammonium, and using non-equilibrium centrifugal extraction instead of precipitation to enrich, recover and separate and purify rare earths. They invented a new technology for efficient and green extraction and separation of ionic rare earth ores, which reduces ammonia nitrogen and radioactive nuclide pollution at the source and efficiently recycles water and materials. It is a brand-new clean production process technology.
There is a problem in the industrial application of new technologies for efficient and green extraction and separation of ionic rare earth ores, that is, conventional extraction equipment is bulky and has low production efficiency, and cannot achieve high flow ratio and high throughput operation. Zhengzhou Tiei Extraction launched a product with independent intellectual property rights - the new centrifugal extractor, which perfectly realizes the high flow ratio industrial rare earth ore extraction, with an extraction rate of >98.5%. This series of centrifugal extractors has been successfully applied in rare earth concentration production lines, which not only solves the technical problems of low resource recovery and utilization rate and serious pollution of three wastes in the process of leaching, enrichment, separation and purification of ionic rare earth ores, but also greatly reduces the operating cost of the equipment.
If you need rare earth extraction equipment, you can contact us for more details.
Email: sales@tieiextraction.com
Whatsapp: +86 19069612820