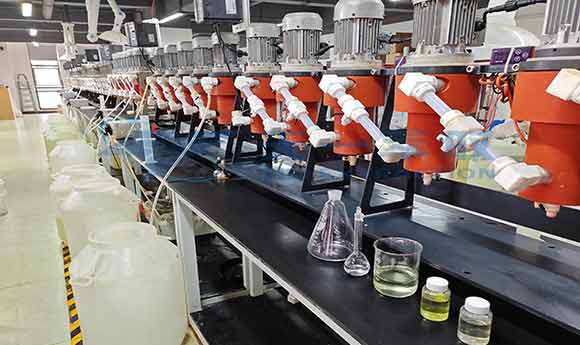
With the increasing attention paid to environmental protection and sustainable development concepts around the world, traditional pyrometallurgy is gradually facing the challenge of being replaced due to its high energy consumption and high pollution. Hydrometallurgical technology has gradually become an important development direction for the metal smelting industry with its advantages of low energy consumption, low pollution and relatively low requirements for ore grade. Solvent extraction technology, as one of the key technologies in hydrometallurgy, is increasingly widely used in copper smelting and other fields. However, solvent extraction systems face a series of complex problems in practical applications. How to effectively identify, analyze and solve these problems is of great significance to improving the production efficiency and environmental protection level of the hydrometallurgical industry.
In practical applications, common problems of solvent extraction systems include unreasonable selection of extractants, unreasonable selection of diluents, prominent emulsification and flocculants, etc. These problems not only affect the efficiency of the extraction process and product quality, but may also lead to equipment failure, environmental pollution and safety accidents.
Solvent Extraction Problem Analysis
1.Unreasonable selection of extractants
The selection of extractants is crucial for the solvent extraction process. Unreasonable selection of extractants may lead to problems such as rapid degradation, more floccules, and severe emulsification during the extraction process. When selecting extractants, factors such as ore type, grade, impurity content, and metal leaching method need to be fully considered to ensure the stability and applicability of the extractants. In addition, the stability of the active ingredients of the extractants is also an important factor to consider when selecting.
2.Unreasonable selection of diluents
The role of diluents in solvent extraction systems cannot be ignored. Unreasonable selection of diluents may affect the solubility of the extractant, the speed of two-phase separation, and interfacial emulsification. High-quality diluents should have lower volatility and lower impurity content to reduce the loss of organic phase and environmental pollution. At the same time, the selection of diluents also needs to consider their impact on the stability of the extractant.
3.Prominent emulsification and flocculant
Emulsification and floccules are one of the most common problems in solvent extraction systems. These problems not only affect the smooth progress of the extraction process, but may also lead to product quality degradation and equipment failure. The generation of emulsions and floccules is related to many factors such as the extraction feed aqueous, extractant, diluent, and operating conditions. Among them, suspended solids, soluble silicon compounds, and organic matter in the feed aqueous are the main factors that lead to the generation of emulsions and floccules. In order to reduce the generation of emulsions and floccules, a series of measures need to be taken, such as optimizing the pretreatment process of the extraction feed aqueous, selecting appropriate extractants and diluents, and controlling operating conditions.
Solutions And Suggestions
In view of the common problems existing in the solvent extraction system, the following solutions and suggestions are proposed:
- Strengthen the screening and development of extractants and diluents: Develop more stable and efficient extractants and diluents for different types of ores and leaching methods to improve the efficiency of the extraction process and product quality.
- Optimize the pretreatment process of the extraction feed aqueous: By strengthening the pretreatment of the extraction feed aqueous, reduce the content of impurities such as suspended solids, soluble silicon compounds and organic matter, and reduce the risk of emulsification and flocculants.
- Control operating conditions: Reasonably control the operating conditions such as temperature, pressure, stirring speed, etc. during the extraction process to ensure the smooth progress of the extraction process.
- Strengthen equipment maintenance and management: Regularly inspect and maintain the solvent extraction system to promptly discover and deal with equipment failures and safety hazards.
- Promote clean production technology: Use clean production technology in the solvent extraction process to reduce the generation and emission of pollutants and improve environmental protection.
As one of the key technologies in hydrometallurgy, the solvent extraction system faces many challenges in practical application. By strengthening the screening and development of extractants and diluents, optimizing the pretreatment process of the extraction feed aqueous, controlling the operating conditions, strengthening equipment maintenance and management, and promoting clean production technology, the problems existing in the solvent extraction system can be effectively solved and the production efficiency and environmental protection level of the hydrometallurgical industry can be improved.
Email: sales@tieiextraction.com
Whatspp: +86 19069612820