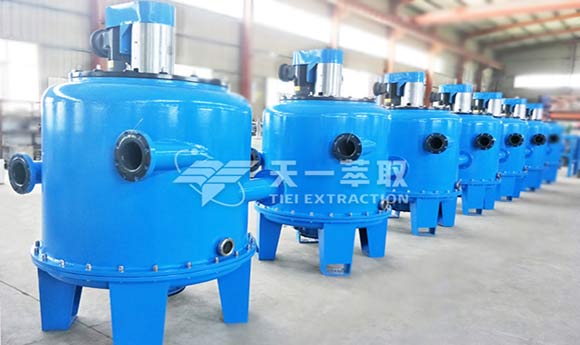
At present, the commonly used methods for treating zinc-containing pickling waste generated in the hot-dip galvanizing industry include neutralization and precipitation, acid distillation method, flotation method, ferrite method, ion exchange method, microbial method, membrane separation method, electrodeionization technology, etc.
Considering that the pickling waste liquid contains a large amount of iron ions, when recovering zinc from the pickling waste liquid, the iron ions present in the waste acid liquid will affect the recovery of zinc. Therefore, when recycling zinc from pickling waste liquid, how to separate zinc and iron is the focus of zinc recovery. This article will introduce how to use centrifugal extraction to separate zinc and iron from pickling waste liquid containing high concentrations of zinc and iron to obtain high-quality zinc products.
(1). Centrifugal extraction process
The centrifugal extraction method is used to separate zinc and iron from the pickling waste liquid, which mainly includes: pretreatment, centrifugal extraction, centrifugal washing, centrifugal stripping, post-processing (precipitation calcination), etc. The control conditions of each process are optimized through small experiments.
- Preprocessing. The pickling waste liquid containing zinc and iron ions is first reduced by iron powder to reduce the ferric iron in the solution. After reduction, the pickling waste liquid is filtered to obtain zinc extraction pre-liquid.
- Centrifugal extraction. The zinc extraction pre-liquid and extraction agent are extracted using a CWL-M centrifugal extractor to obtain zinc chloride-loaded organic and raffinate liquids.
- Centrifugal washing. The load organic uses acidic washing liquid and the CWL-M centrifugal extractor to wash impurities, obtain the washed organic phase and washed aqueous phase.
- Centrifugal stripping. After washing, the organic phase is stripped with an alkaline stripping agent to obtain regenerated organic and zinc stripping rich liquid, and the regenerated organic phase can be recycled.
- After precipitation and calcination, the product high-purity anhydrous zinc chloride is obtained. The stripped rich liquid is deoiled and enters the pH adjustment tank, where the zinc dichloride diammine precipitate is obtained in a pH adjustment tank; the zinc dichloride diammine precipitate is filtered, dried, and calcined to obtain high-purity anhydrous zinc chloride, and the ammonia is recovered.
(2). Advantages of centrifugal extraction process
The centrifugal extraction method is a green extraction process developed in combination with the new CWL-M extraction equipment. It can obtain high-quality anhydrous zinc chloride products from acidic waste liquid containing zinc and iron ions. Has the following characteristics:
① High metal extraction rate, up to 99.9%.
②Simple process and easy operation.
③The quality of the stripping liquid obtained is stable and can meet different production requirements.
④The residual amount of aqueous solvent after treatment is small, which can reduce the processing pressure of subsequent sections.
⑤The extraction equipment occupies a small area and has great processing flexibility.
Email: sales@tieiextraction.com