Centrifugal contactors, like mixer-settlers, are discrete-stage units, providing one stage of
extraction per unit and are readily linked together as each rotor pumps separated fluids to the
next stage inlet in each direction. The primary difference between a centrifugal contactor and a
mixer-setter is the separation of the two-phase mixture. Centrifugal contactors employ a
spinning rotor that 1) intensely mixes the two phases and 2) separates the two phases inside
the rotor where the centrifugal forces can be as high as 300 g, resulting in efficient and fast
phase separation. The separated phases exit the contactor by overflow and underflow weirs,
similar to a mixer-settler.
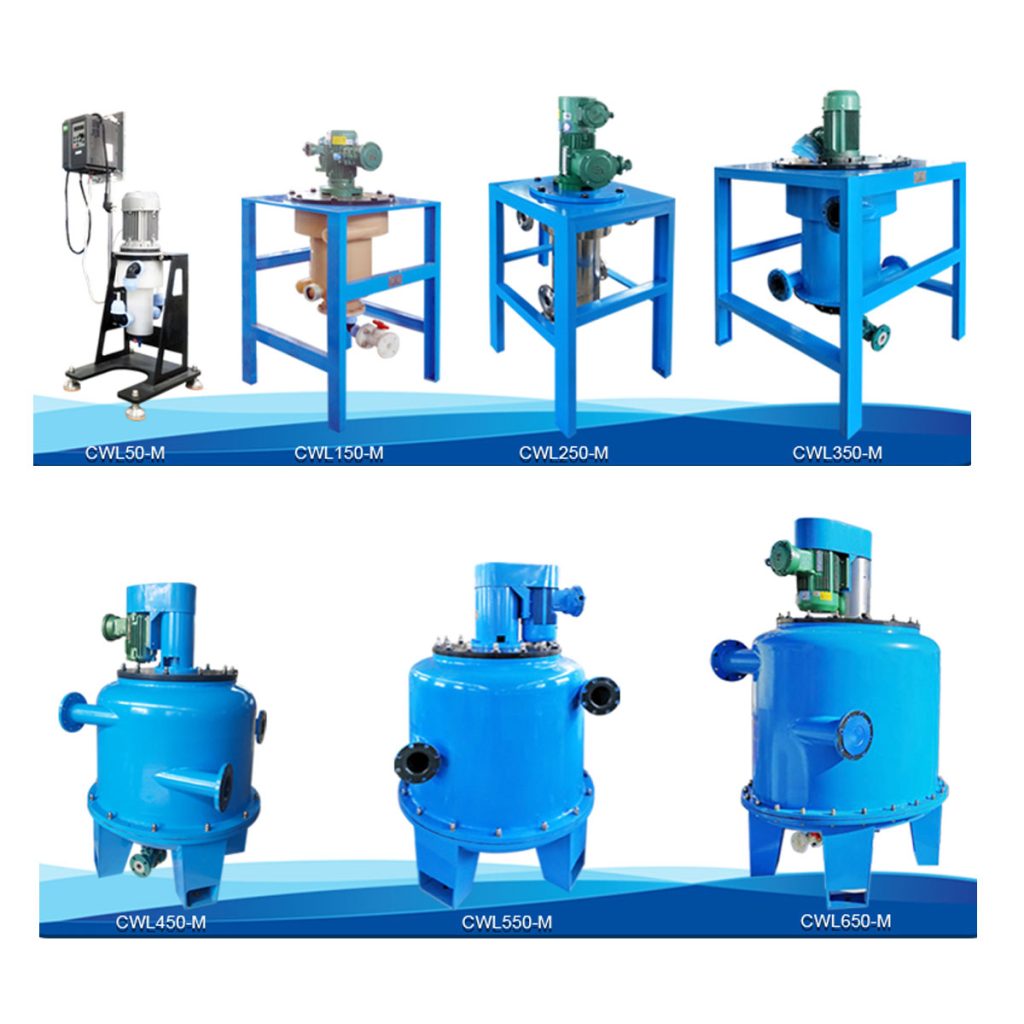
Centrifugal contactors have high single stage efficiency (routinely greater than 95% of
theoretical for chemical processes with rapid kinetics). Process flow interruptions cause no loss
of process concentration profiles if centrifugal contactor rotors are kept spinning. Centrifugal
contactors require a minimum of instrumentation for process operation. Computer control via
commercial software allows monitoring of motor amperage, rotor rpm, inlet flow rates,
temperatures and many other process parameters. Centrifugal contactors are used when a
process requires short residence times, on the order of several seconds. They require a small
facility footprint, and minimal headspace, but do require remote maintenance capability, for
periodic removal of the motor and/or rotor.
Centrifugal contactors have been the subject of much recent development work. This precluded removal of the rotor assembly, and so the annular centrifugal contactor was developed, which allowed the
motor and rotor assembly to be easily removed. Other designs included multistage units, units for low-mix applications (higher phase separation), and clean-in-place units that have an array of internal spray nozzles to facilitate solids removal, if necessary.