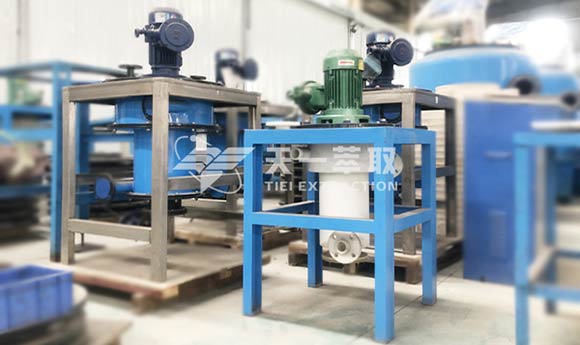
As the cathode materials of lithium-ion batteries develop from single lithium cobalt oxide or lithium manganese oxide to nickel cobalt lithium manganese oxide ternary materials, the purity requirements for manganese sulfate have increased significantly, and the impurity content of K, Na, Ca and Mg must be controlled below 5.0×10⁻³%. Removing Ca and Mg from manganese sulfate is one of the key challenges. Traditional methods such as crystallization require multiple crystallizations, resulting in low manganese recovery rates; electrolysis has a complex process and high energy consumption; chemical precipitation uses fluoride, which is costly and produces waste residue. In contrast, solvent extraction is favored for its simple process, low energy consumption and high efficiency. Commonly used organic phosphoric acid extractants such as P204, P507 and Cyanex272 are used. Laboratory studies have shown that these extractants can effectively separate Mn from Ca and Mg, and obtain high-purity manganese sulfate solutions through sulfuric acid stripping. However, laboratory studies are greatly affected by operational factors and are difficult to directly apply to industrial production.
Traditional reactors and mixer settlers have problems such as long residence time, small phase interface contact area and difficult phase separation, which limit the expansion of production capacity. Centrifugal extractors have the advantages of less material retention, short residence time, high mass transfer efficiency and rapid establishment of phase equilibrium, making them more suitable for large-scale production.
Process flow of manganese sulfate purification using CWL-M centrifugal extractor
1.Centrifugal extraction: The feed liquid (a solution containing a certain concentration of manganese (Mn), which may also contain manganese (Mn) impurities such as calcium (Ca) and magnesium (Mg)) enters the centrifugal extractor from the heavy phase inlet, and at the same time, the pre-saponified extractant (such as P204 or Cyanex272) enters from the light phase inlet. The two phases are countercurrently contacted under high-speed rotation, so that Mn is transferred from the aqueous phase to the organic phase.
2.Centrifugal washing: The organic phase loaded with Mn then enters the washing section, and is countercurrently contacted with a dilute sulfuric acid solution to remove Ca and Mg impurities.
3.Centrifugal stripping: The washed organic phase enters the stripping section again, countercurrently contacted with the sulfuric acid solution, and Mn is transferred from the organic phase back to the aqueous phase to obtain a pure manganese sulfate solution.
Process advantages of manganese sulfate purification using CWL-M centrifugal extractor
1.Efficient mass transfer: The CWL-M centrifugal extractor uses the strong centrifugal force generated by high-speed rotation to fully mix and quickly separate the two-phase liquid, greatly improving the mass transfer efficiency. Compared with traditional reactors or mixer settlers, it has a fast processing speed, short residence time, and can achieve a higher extraction rate.
2.Low material loss: Due to the reasonable internal design of the equipment and the small amount of retention, the loss of the organic phase is very small during the entire extraction process, thereby reducing production costs.
3.Easy to operate and maintain: The CWL-M centrifugal extractor has the characteristics of high degree of automation, simple operation, easy control, small footprint, and easy installation and maintenance. This not only saves labor costs, but also reduces operational errors caused by human factors.
4.Environmental protection and energy saving: The entire process produces almost no wastewater and waste residue, which is in line with the concept of green production. In addition, low energy consumption is also a highlight, which helps to reduce the operating costs of enterprises.
5.Strong flexibility: According to different processing volume requirements, CWL-M centrifugal extractors of different specifications and models can be selected to meet various application scenarios from small-scale laboratory research to large-scale industrial production.
Practical application cases using CWL-M centrifugal extractor
In one experiment, when the Mn concentration in the feed liquid is 29.51 g/L, the extraction ratio (O/A) is adjusted to 3.0:1.0, and after four-stage centrifugal extraction, a Mn extraction rate of up to 98% is finally achieved. Subsequent centrifugal washing and three-stage centrifugal stripping steps further purified the product, so that the Mn²⁺ concentration in the stripping liquid reached 9.16 g/L, while the Ca²⁺ and Mg²⁺ contents are reduced to 2.19 mg/L and 3.34 mg/L, respectively, which fully met the standard requirements for battery-grade manganese sulfate.
With its excellent performance, the CWL-M centrifugal extractor has shown great potential in the preparation of battery-grade manganese sulfate. It can not only effectively improve the purity of the product, but also significantly reduce production costs. It is an ideal choice for the future manufacturing of lithium battery positive electrode materials. For companies seeking high-quality, low-cost solutions, the CWL-M centrifugal extractor is undoubtedly an ideal choice.
Email: sales@tieiextraction.com
Whatsapp: +86 19069612820